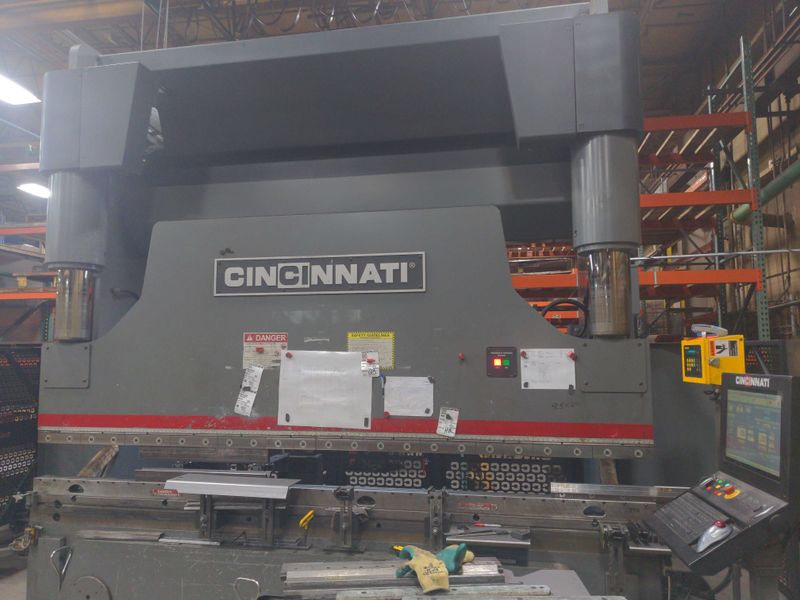
Press Brake Maintenance Benefits
A press brake needs to be down during maintenance; unfortunately, this results in many companies skipping press brake maintenance. This also means these companies miss out on the benefits of regular press brake maintenance:
- Precision and Consistency: Press brakes rely on precise adjustments and alignments. Any deviation can result in inaccuracies in bending angles and dimensions, leading to quality control issues, rejected parts and the cost of rework.
- Safety: Inspection of a press brake’s safety features is a routine part of maintenance. When maintenance is not performed regularly, it increases the risk of workplace accidents due to worn or malfunctioning parts. The latter risk, of workplace accidents, is in itself a reason to regularly schedule press brake maintenance. According to the National Safety Council, these accidents cost US companies more than $167 billion in 2021. A well-maintained press brake is a safer and less costly one.
- Cost Efficiency and Less Chance of Downtime: Proactive maintenance can extend the lifespan of the press brake, reduce downtime and lessen the chance of lost productivity. Simply, it's more cost-effective to invest in regular maintenance than to prematurely replace parts or, worst-case scenario, the whole machine.
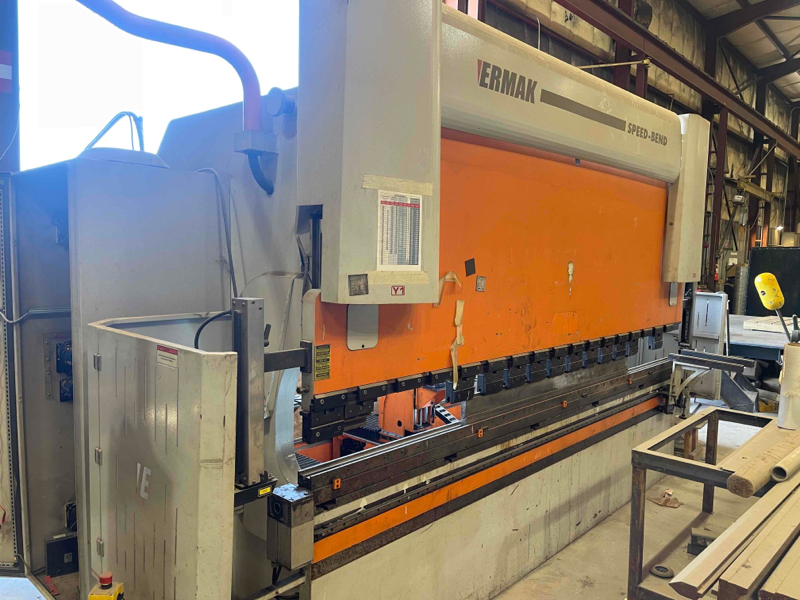
Press Brake Maintenance Tips
Press brake maintenance is a step-by-step process that involves accessing, inspecting, and servicing key parts of the machine:
- Lubrication: Adequate lubrication is vital to reduce friction and wear on moving parts. Components like ball screws, guides, and bearing should be inspected and lubricated.
- Hydraulic System: During press brake maintenance, it is important to check for hydraulic fluid leaks. If the fluid is low, it should be filled to the correct fluid level and the reason for the leak should be identified. Basically, all hoses and seals should be in good condition to prevent system failures; if not, the issues should be noted, and repaired or replaced.
- Electrical Components: All electrical connections, switches, and controls should be inspected and checked regularly. Loose connections and damaged wiring can lead to electrical issues.
- Tooling Inspection: All tooling needs to be examined, including the punch and die, for signs of wear or damage. Replacing worn tooling ensures consistent and high-quality bends. Press brake tools can last longer with proper storage, cleaning and light lubrication, and the consistent wearing of gloves (by the operator).
- Backgauge and Crowning System: The backgauge system needs to be well-calibrated regularly and free from debris. If the press brake has a crowning system, the system needs to be checked and properly adjusted to maintain uniform bending along the entire length of the sheet.
- Cleaning: A regular press brake cleaning removes dust, chips, and debris. Cleanliness helps prevent contamination of critical components and ensures smooth operation.
When issues are found during the maintenance process, they should be documented, repaired on-the-spot or flagged for future follow-up. If a maintenance company is utilized, they should take care of the documentation. All maintenance records should be contain the date of maintenance, what maintenance was done, and any repairs or replacements that were performed during the process.
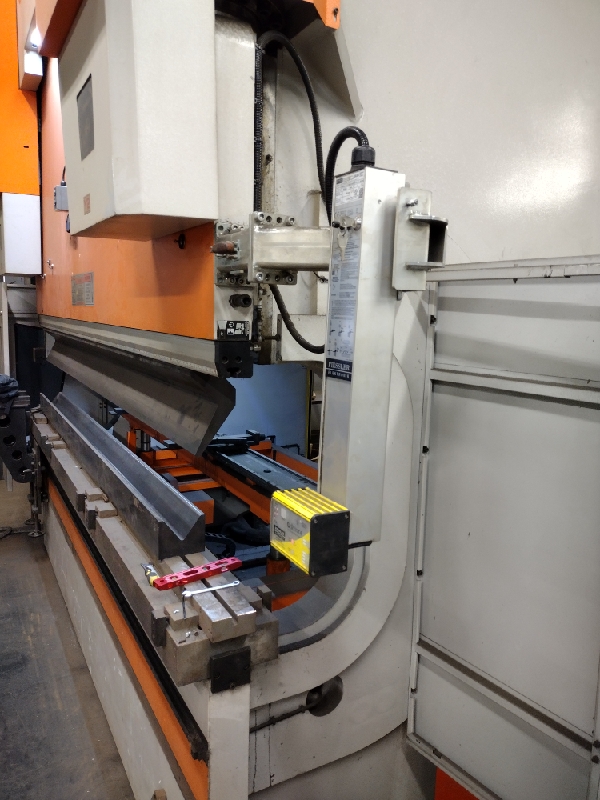
Importance of Regular Maintenance
Press brake maintenance yields many benefits if it is performed regularly, which is why a maintenance schedule is so important. A maintenance schedule ensures that staffing is available, that issues found during maintenance are documented for future follow-up, and that there is scheduled time for shut-down. If the schedule cannot be maintained, companies can contact a quality maintenance company to fill in gaps or manage their maintenance schedule completely.
The schedule of press brake maintenance should be set based on the manufacturer’s recommendation and machine usage. Whenever that is, it’s important to schedule this critical part of machine ownership because it extends the life of the machine, prevents costly workplace accidents, and maintains optimal bending precision and accuracy.