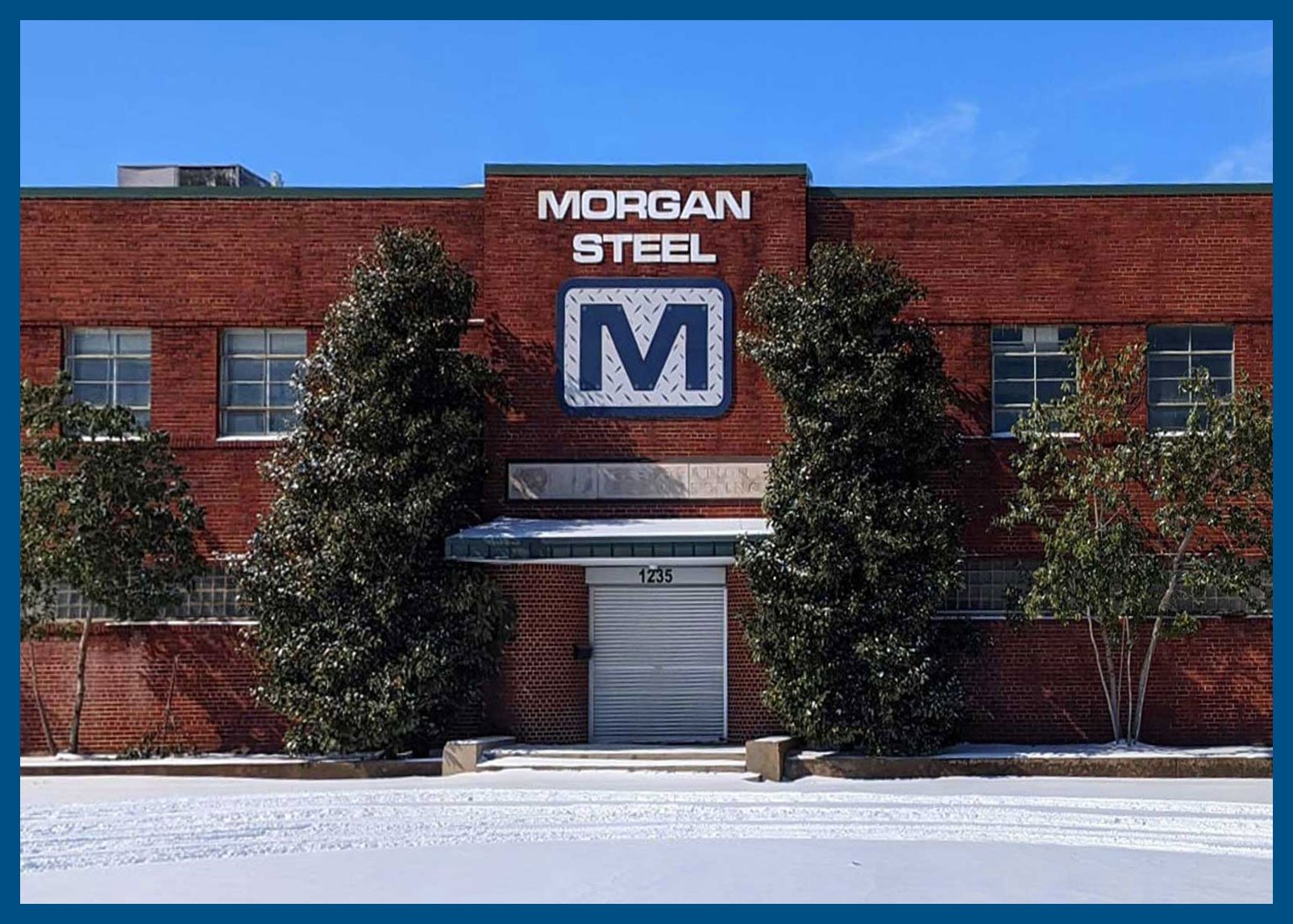
About Morgan Steel
Morgan Steel is a Southern giant in the metal acquisition and fabrication industry. The company utilizes eight powerful fiber lasers to process material and moves an impressive one million pounds of material each day. However, their rapid growth and expansion led to a need for new equipment and relocation services to optimize their operations.
The Challenge
Over the years, Morgan Steel added several nitrogen generation units and air compressor systems to their facility. While these additions were necessary for business growth, the systems were not installed strategically or organized within the facility. The result was an operational space with a layout that was becoming increasingly difficult to manage. Morgan Steel’s leadership team knew they had to make a change when two more nitrogen generation systems were set to join the current setup.
The Solution
After an extensive evaluation, Morgan Steel’s team drafted a layout that maximized productivity. OpEx Service was contacted to manage this huge equipment relocation. The massive project called for the relocation and installation of four nitrogen generation systems, six 400-gallon air tanks, four desiccant air dryers, six 50HP air compressors, plus securing all needed equipment for the project and managing electrical and plumbing installations.
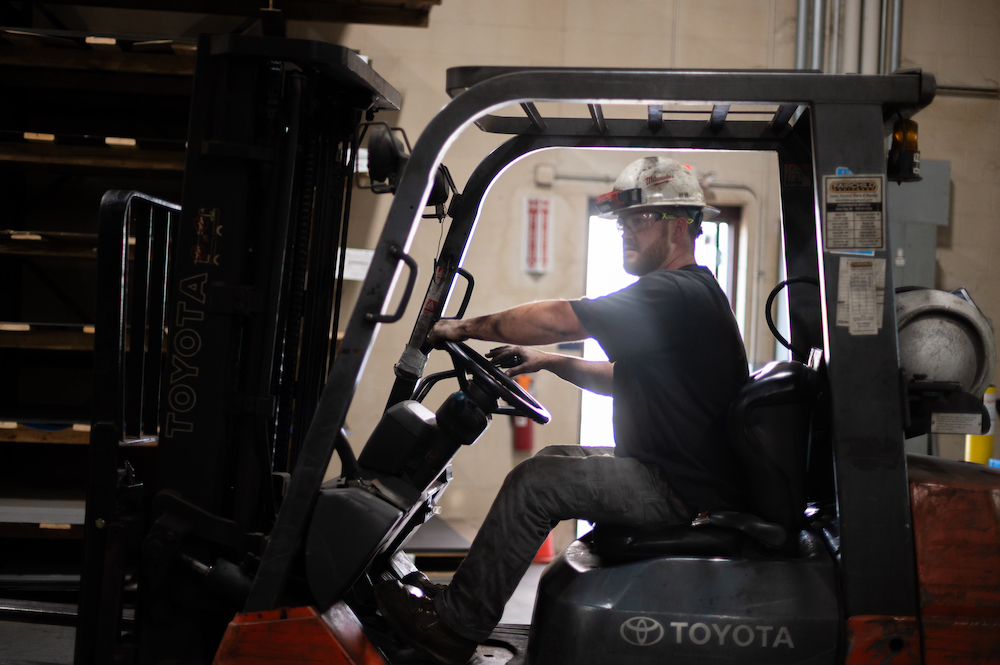
The Outcome
OpEx managed every step of the project and took the plan from draft to fruition. The project result was a space with a more efficient layout that was easier to clean, manage and maintain. The air compressors were relocated to minimize noise and heat production within the building, while the plumbing system was upgraded with ball valves at all nodes for easy isolation of components. Additionally, a cable tray system was installed for all existing equipment with space for future cable management needs.
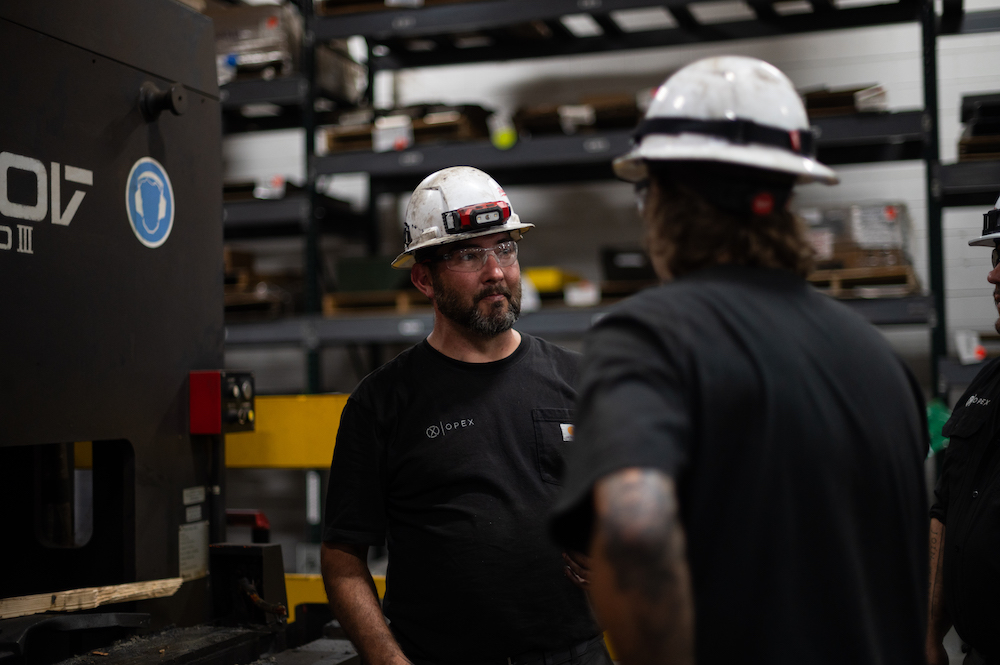
The OpEx team also ensured that there was ample room on the floor and upgraded their electrical systems to accommodate the new nitrogen generation systems and future equipment, setting Morgan Steel up for future growth with additional equipment acquisitions.
Looking Ahead
This case study highlights OpEx Service's capability to provide comprehensive solutions for complex customer projects, beyond standard machine maintenance and repair. It showcases how effective planning and execution can result in operational excellence, setting the foundation for continued customer business growth.